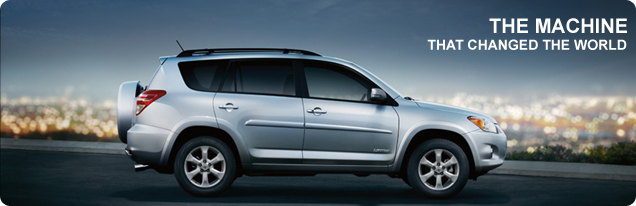
By Oskar Olofsson, 2010
※5S§ is a method to create a safer, cleaner, and better-organized workplace, using five Japanese words:
• Seiri 每 ※Sort§
• Seiton 每 ※Set in Order§
• Seiso 每 ※Shiny Clean§
• Seiketsu 每 ※Standardized Cleanup§
• Shitsuke 每 ※Sustain§ (sometimes ※Sustained Discipline§)
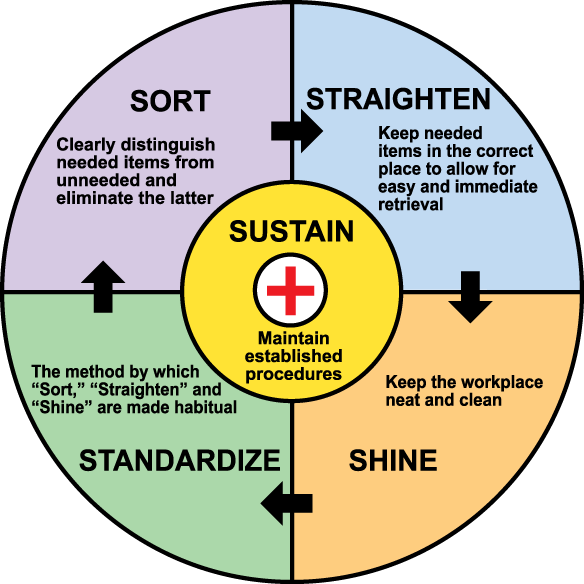
Fig 1. "5S" System
This article is a basic introduction and overview for each of these steps, which should be followed in sequence. Later articles cover each stage in more depth.
It is possible to start a 5S program in just one department or area. This allows management to fine-tune the approach and adapt it to the specific workplace.
Running a pilot project also permits a group of employees to learn what to do and how to do it. For example, suppose a factory has a centralized team for equipment maintenance, but separate workers for various processes. The maintenance team will be involved everywhere. They might be overwhelmed by an initial factory-wide project, but do well in one area at a time. Also, once they learn from the pilot project, they will bring their new expertise to each new area.
Seiri 每 ※Sort§
Seiri means ※to sort§ or organize. It is the first stage of the 5S method.
Sorting is a team activity. Production and maintenance workers should carry this out together.
The goals of Seiri are:
• Remove unnecessary objects
• Reduce waste
The basic tool is a red tag: tag the item, allow a month for someone to make a case for keeping that item; and discard the item after that month.
The additional tool is the 5S Sort List: a log to follow up every red tag.
Remove unnecessary objects
This phase should identify and eliminate things like a bin of parts that were rejected and will never be reworked; broken or ※custom§ tools 每 anything jerry-rigged from string and duct tape; obsolete spare parts, inventory, and even documentation or binders.
If you don*t need it: sell it or scrap it. If you need it but it is broken or hazardous: fix it properly.
Reduce waste
This identifies the hindrances, and goes beyond simple ※waste material§:
• Do we lack work instructions that are available, accurate, and used?
• Are there hazards: clutter; missing safety guards; electrical faults; broken steps on ladders?
• What environmental hazards are we tolerating? Look for solids, liquids, gasses, and dust.
• Are tools broken, missing or inadequate?
• Are workbenches at the right height? Are chairs too low for some workers? Where have back injuries occurred?
• Where has maintenance been neglected 每 whether for equipment or buildings?
Seiton 每 ※Set in Order§
The principle here is to keep things in their proper places. One guide to proper placement is to keep frequently-used items handy, and store other things where they can be found.
On a personal level, you might carry a pen in your pocket because you jot notes all day. You keep your winter coat in a closet at home during the summer. Another example is how you should arrange your kitchen. You probably have cutlery sorted in one convenient drawer; the frequently-used pots and pans handy; but the once-a-year fondue set is tucked out of the way.
Seiton uses the same concept, expressed for a workplace:
• Keep tools near the place they are used
• Don*t make workers bend or stretch frequently
• Store rarely-used items where they won*t get in the way, but where they can be found easily
The only exception to ※store rarely-used items§ would be for safety gear. Hopefully you rarely need a fire extinguisher or eye-wash station 每 but when you need it, it should be handy.
The Seiton article has more details on how to progress from identifying, through planning and implementing the ※Set in Order§ process.
Seiso 每 ※Shiny Clean§
This is the exception 每 the only one-time activity in the 5S method.
This stage has two goals:
• Determine and gain agreement on the desired level of cleanliness
• Learn how to make new routines so this will become standardized (in the Seiketsu stage)
Several questions help this stage to be more than just ※polish until it shines for inspection§:
• How much cleanliness is required for safety, for ease of use, and to minimize equipment breakdown?
• How clean should the environment be for comfort and morale?
• How will cleanliness improve product quality?
• While cleaning, do we notice maintenance issues that should be addressed?
This is also a team exercise. Clean and inspect one area at a time: equipment; work stations; and common areas. Take notes to guide future work. Finally, take photos of the ※shiny clean§ workplace to illustrate the new standard.
Seiketsu 每 ※Standardized Cleanup§
This phase draws on the notes from the Seiso stage. Consider the sources of dirt: air-borne dust; sawdust or other dry powder from cutting operations; splatter from wet processes; or simple trash because there is no proper container.
The results include:
• Maintenance for buildings or equipment, if these are sources of dirt
• Improvements to processes 每 for example, adding a dust hood over a cutting area
• A binder with instructions for cleaning each work area
• A checklist for each cleanup period (daily, biweekly, or less frequently)
• A list matching the people with their responsibilities
A practical target is to have all workers take five minutes every day to tidy up after themselves 每 including the time to complete and sign the checklists. By dividing the work among all the employees:
• No-one has a huge burden
• No-one seems unproductive
• Morale improves because everyone has a common purpose
Supervisors should monitor compliance with Seiketsu. The checklists make this both important and achievable.
Shitsuke 每 ※Sustain§
Shitsuke is a complex Japanese concept that includes instilled discipline, self-discipline, common cultural values, and self-motivated practice to improve. A Westerner might think of: parents training their children to brush their teeth after each meal; children then brushing regularly; expecting everyone to brush after meals; and (for a non-dental example) golfers continuing to practice putting, even though the stroke may seem easy to a beginner.
This step requires continued management support and communication.
Benefits of 5S (Lean Manufacturing)
What is 5S?
※5S§ or "Lean 5S" is a method to promote a safer, cleaner, and better-organized workplace 每 often a factory, but the 5S method can be applied to almost any work environment:
• Office space 每 from cubicles to mail rooms to library space
• Computer or server rooms, including online files and folders as well as physical objects
• Work bench areas
• Warehouses, storage sheds and outdoors storage areas
• Hospitals and health care facilities
If an area can become messy, cluttered, disorganized, hazardous or dirty 每 5S can improve it.
The 5S method is not a one-shot cleaning campaign. 5S leads to a new quality standard which results in sustained improvements. As well, 5S provides the methodology and discipline to live up to the new standards.
5S should spell the end to one-time cleanups and is a part of, and often the first step in Lean Manufacturing implementation.
How will a 5S program benefit my workplace?
The bottom line is that 5S should result in greater profits#but let*s look at some interim benefits first.
Each aspect of 5S can lead to both immediate and long-lasting benefits. Later articles deal with some benefits in greater detail, but here is a quick sample to whet your appetite.
5S addresses safety by making a workplace neater and more orderly. This reduces the risk of injuries, in both the short and long term. For example: in the short term, workers are less likely to trip over misplaced items or injure themselves on equipment lacking proper safety guards.
A neat workplace means that frequently-used tools are stored close to hand, resulting in less time wasted searching for misplaced items. Likewise, workers do not need to sift through clutter to find the specific tool or spare part needed at that moment.
In some environments, greater cleanliness will result in less dust or other airborne contaminants. This may lead to fewer chronic health issues.
Cleaner equipment may mean fewer malfunctions or breakdowns. Even in the short term, a daily five-minute cleanup can eliminate plant-wide cleaning binges required before a major customer arrives for a tour.
Over the long term, optimized workflow may result in fewer chronic ailments such as sore backs or RSI (repetitive stress injuries).
Every day, optimized workflow should result in quicker operations 每 whether it is a worker moving a piece directly to the workbench, or a forklift driving in a straight line rather than wending a path among cluttered piles of inventory.
5S can improve morale in several ways. Most obviously, workers and managers can take greater pride in a clean and orderly workplace. As well, every employee will have responsibilities and duties aimed at a common goal 每 to maintain the 5S standards 每 which leads to a sense of teamwork and shared vision.
Finally, a 5S program can be a stepping-stone for later initiatives such as Lean Manufacturing or Continuous Improvement.
How can these 5S changes improve profits? Here are some of the ways:
• Both fewer injuries, and fewer long-term illnesses, lead to a reduction in lost time, compensation, and scrambles to train workers to cover for colleagues
• Less time spent searching for misplaced tools or parts means higher productivity
• Cleaner equipment may mean less downtime for repairs or maintenance, and also savings on replacement parts
• Optimized workflow leads to higher productivity due to time savings
• Optimized workflow leads to higher productivity by reducing process errors and re-work
• A cleaner workplace may result in cost savings for janitorial staff
• Obsolete equipment or parts may be sold
• Reduced inventory 每 whether equipment, spare parts, or raw materials 每 may result in reduced warehouse costs
As a rule of thumb: a workplace can achieve a 10% increase in productivity after completing a 5S program. It does depend on the initial state of affairs: the worse when you started, the greater the improvement.
The bottom line is that 5S is good for your bottom line.
Follow Up
Audit and certification programs should be introduced to follow-up once the whole factory has undergone a 5S program.
Lean 5S - The Audit Process
The three purposes of conducting regular 5S Audit reviews are:
• Review compliance to the 5S standards for your factory
• Note and address non-compliance 每 to fix what is wrong!
• Provide a formal opportunity to suggest improvements
The Basic Steps
Plan for the audit by dividing the workplace into various areas, probably the same ones where different teams conducted the various 5S stages. Make a checklist for each area, based on the standards that were set during 5S.
You also need the list of known problems in each area. From the initial 5S sweep, this may include:
• Machines needing repair
• Tool racks
• Signage on tool racks or cabinets or storage shelves; warning signs; ※keep clear§ markings for corridors; or instruction pages
• Surplus equipment or materials which were not immediately removed
During the audit, there are really only three key tasks:
• Determine whether known problems have been addressed:
o Does this machine still leak lubricants?
o Has the required tool rack been installed in this area? Is it labeled? Is it full? Are tools still left on workbenches?
o Is the warning sign in place so people will not walk under this crane?
o Why is this outdated drill press still in the corner?
• See that standards are being met:
o Are tools left on workbenches?
o Is something missing from a tool rack?
o Is dirt accumulating somewhere?
o Are existing labels still visible and easily read? (This is especially important for signs that may be obscured by dust, and for lines painted on floors where they can be scuffed)
o Are there new sounds or smells that indicate that gears are grinding or fluids are leaking?
• Note what has not yet been standardized 每 this is the most creative and difficult part, because it may involve seeing what is missing in an area that seems tidy:
o Why is there no sign over the neat stack of work-in-process materials on that shelf? (How will the next shift know what is there, or what should go there?)
o Tools that are not yet labeled
o Is there a limit to how high those barrels can be stacked? Why don*t we show that information on the sign for that storage area?
o Do we need all those cans of wing nuts in this assembly area? How many are used in one day? Should the rest of the month*s supply be stored elsewhere?
Safety infractions should also be part of the 5S audit:
• Are WHMIS (Workplace Hazardous Materials Information System) labels used properly?
• Are fire exits visible and clear? Are the fire extinguishers charged and inspected on schedule?
• Are stairs and ladders safe?
• Do we notice unsafe behavior regarding heights and falls? Climbing a ladder without maintaining three points of contact? Working on a height without the required safety tether?
To follow up on each 5S audit:
• Write up a work order to deal with each deficiency
• Update the next check list:
o Check off what was corrected
o Add new deficiencies to be reviewed
• Determine the score:
o Deduct for each deficiency
o Add a point for each correction
o Add a point for each suggestion for improvement
o If the previous audit had found deficiencies, the goal is to eradicate them
o The ultimate goal is to regularly achieve zero outstanding deficiencies
How often should audits be performed? Regular audits lead to the best results:
• Weekly ※self-check§ audits by teams of workers, reviewing their own areas
o This might be the best way to generate suggestions for improvements
• Monthly audits by the area supervisor
o Ensure that the weekly audits catch any problems with the daily or weekly cleanups
o Pay special attention to the less-frequent cleaning tasks
o Try to notice what is missing: new tools that do not yet have a place in a rack; materials stored neatly but not well-labeled
• Quarterly audits by the plant manager
o Ensure that standards are being met
o If there are deficiencies, ask ※why§: try to determine the root causes
o Ensure that resources are allocated to repairs and to making the long-term improvements
Without audits, it is impossible to ensure compliance.
Lean 5S: The Certification Process
5S Certification may be as informal as making your own award when your workplace first passes its internal 5S Audit, but it is an important component in having a complete and successful 5S environment.
The purpose of performing 5S Certification is to visibly demonstrate both progress and compliance. This is especially important to make improvements in a large workplace with many employees.
Planning is important: agree on the criteria for awarding a 5S certificate. The criteria should be strict enough that it will require significant effort to achieve certification. If you don*t award the certificate the first time 每 because there still are deficiencies 每 that will enhance the credibility of the process.
As in prior 5S phases, appointing a team is a necessary step. The people should know the workplace and the 5S goals well, care about the details, and be respected as authorities in the workplace.
Publicize the process and report regularly on the progress. Some ways to do this are:
• Set up a notice board to indicate progress
o A ※thermometer§ rising to show increased compliance
o A map of the plant, with each area changing to green when it meets the target
o Show progress in a ※Plan-Do-Check-Act§ circle for each department
• Set up a page on your internal website 每 include as much detail as you want to maintain over time
Design a great diploma and display it prominently. You may want to plan for periodic re-certifications 每 set aside a place on the diploma for additional annual gold seals, for example.
External consultants are normally not prepared to offer a stand-alone 5S Certification.
However, 5S is a fundamental part of TPM (Total Productive Maintenance). The JIPM (Japan Institute of Plant Management) does offer a ※TPM Award§ for excellence. If your company pursues TPM, earning this award would be a significant achievement and a clear indication of 5S compliance.
» More Information